
The US warehousing and goods transport sectors have been under enormous pressure over the past 18 months.
An unexpected explosion of demand, a shortage of port workers due to the Covid-19 pandemic, an absence of available chassis to move freight and a weakened transportation infrastructure for inland movements have combined to cause US companies to fail to meet production, delivery and distribution targets.
The result is swamped warehouses and a consequent increase in traffic at ports as containers wait for days, rather than hours, to offload goods. To further complicate matters, the country suffers from a lack of additional logistics space that would help alleviate some of this pressure.
“The disruptions caused by the pandemic have led to an increased focus on building more resilient supply chains,” says Melinda McLaughlin, global head of research at warehousing investment trust Prologis. “Combined with the societal shift to e-commerce, this has fuelled record demand for logistics real estate.”
A recent survey conducted by Prologis estimates that available logistics space in the US will dry up in 16 months’ time, meaning some time around late 2023. “The expansionary average is 36 months, and anything less than 50 months is consistent with positive real rent growth,” the report says.
McLaughlin adds: “Vacancies are at historic lows in the US as companies move to online fulfilment models and higher inventories. Intense competition for warehouses is pushing rents higher than ever, and we expect this to continue into next year.”
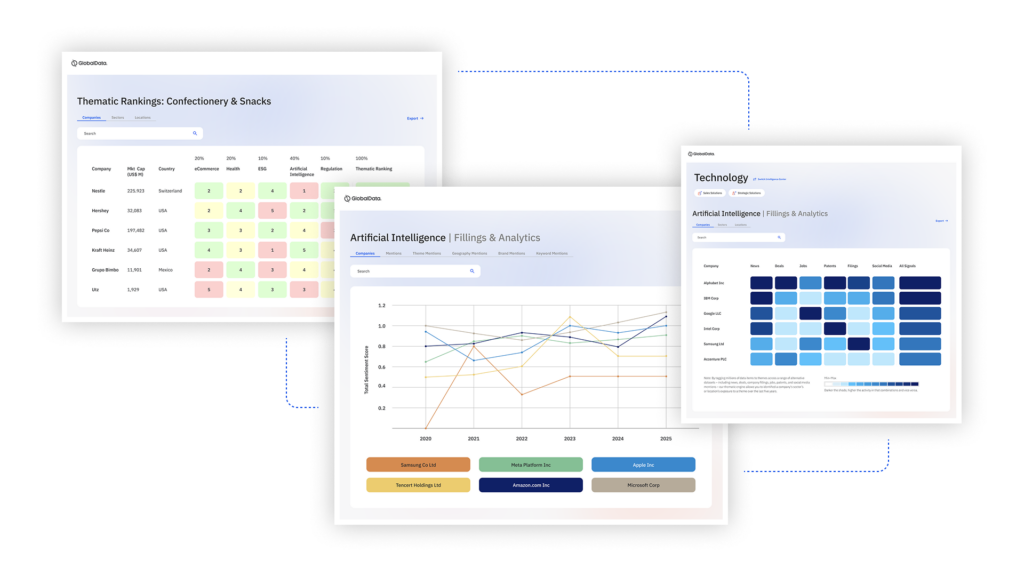
US Tariffs are shifting - will you react or anticipate?
Don’t let policy changes catch you off guard. Stay proactive with real-time data and expert analysis.
By GlobalDataRent up, supply down
Competition for space led to record first-quarter rent growth in the US in 2022 as rents increased 8.5% quarter over quarter, the Prologis report shows.
While demand for more logistics is high, supply is low and this has led to reduced absorption. “Logistics customers absorbed 88 million square feet in the first quarter of 2022, down from about 120 million square feet in the prior quarter,” the survey says. “Materials shortages are fuelling this scarcity. New supply in the first quarter of 2022 was lower than expected, at 68 million square feet. The vacancy rate fell by 20 basis points from the prior quarter to a record low of 3.2%.”
To address the issue of overwhelmed warehouses, some large retailers have added capacity to impressive rates. The New York Times reports that Amazon spent more than $164m to construct new warehouse space in 2021, while home improvement retailer Lowe’s spent more than $17m.
The situation has also created issues at the manufacturing stage as manufacturers have had to come up with quick fixes.
“Most manufacturers – whether at the input or final goods level – have embraced just-in-time production models and only maintain a small cushion of available inventory to meet manufacturing requirements,” says Jeremy Page, founding partner at trade law firm Page Fura.
“Delays in port arrival, offloading and onward movement have caused reductions in production shifts, the periodic shutting down of entire lines or factories and the rationing of parts to those products or models either highest in demand or in realised profit.”
How is the Biden administration responding to the supply chain crisis?
The Biden administration has not been sitting idly by as supply chains in the US undergo this period of volatility, and has set up the Supply Chain Disruptions Task Force to act as a broker to coordinate the job that companies, workers and other players are facing to find solutions.
The November 2021 report from the task force highlighted that demand for goods in the US remains abnormally high, with the number of container ships waiting to dock at the Ports of Los Angeles and Long Beach – which together handle 40% of containerised imports entering the country – being much higher than average.
Between January and September 2021, more than seven million loaded containers were imported, 18% higher than over the same period in 2018, which had been the previous record, the chart below from the White House’s briefing shows.
Despite this supply chain volatility, however, store shelves are now back to pre-pandemic levels.
One of the factors putting pressure on the US warehousing and goods transportation sectors is the neglected and ageing infrastructure that underpins the sorting out and distribution of goods that come into (and then have to travel through) the country.
“As US consumers continue to purchase goods at a high level, decades of neglect and underinvestment in our infrastructure have left the links in our goods movement supply chains struggling to keep up with the rapid and persistent increase in goods movement that the pandemic has generated," a White House briefing said. “This poses a collective action problem in the largely private system that moves containers of goods from ships to docks to trains and trucks to then be distributed to warehouses, factories and stores.”
To help address the issue, Joe Biden issued a call to action to encourage every link in the goods movement chain to move towards a 24/7 pace to increase the volume and speed at which products flow through the system.
The Ports of Los Angeles and Long Beach, along with International Longshore and Warehouse Union workers, acted first in committing to try a new solution. Some of the countries’ largest companies joined in as well, among them Walmart, Target, FedEx, UPS and Home Depot.
Since then, others have joined in the response. The State of California stepped up, issuing an executive order to identify state-owned sites to serve as temporary warehouses and allow trucks to carry more goods.
The City of Long Beach then helped create more storage space through a temporary zoning change to facilitate container storage. In mid-May, Union Pacific, one of the two major railroad companies responsible for moving goods out of the port, announced it would operate its station near the ports 24/7 and offered discounts to customers for each container they moved by rail.
In addition, the US Department of Transportation and the State of California announced a $5bn partnership to modernise California’s goods movement chain, strengthening the capacity and resiliency of the country's key import and export hub. The results of these combined efforts will be more space available to store containers and faster paths for containers to exit and enter the ports.
“We need to seize this moment to strengthen our country’s future competitiveness by focusing longer term on building the resilience of our nation’s supply chains," stated the White house briefing. "That includes a goods movement chain that is more resilient, fluid and can operate at a higher velocity.
“For too long, our country has underinvested in the roads, railways, ports and projects that propel goods movement. With the Infrastructure Investment and Jobs Act, we can make the fundamental changes that are long overdue for our ports, rail and roads. This is how we build back better, with government bringing workers and businesses together to leverage American ingenuity to tackle the challenges brought on by a pandemic.”
The new normal and how to get there
Building resilience across supply chains to ensure that future shocks are absorbed better has been a leitmotif in the industry, on a global scale, ever since the Covid-19 outbreak.
Until then, supply chains had been built around the concept of efficiency rather than resilience and sustainability, meaning production was often happening far away from the country of distribution and at much cheaper price, and goods were being shipped across the world.
As the pandemic, along with other so-called black swan events such as the Suez Canal obstruction, Brexit and more recently energy and other materials shortages, has highlighted, such models are no longer suitable.
But what does resilience mean and how is it possible to achieve it?
According to Christian Lanng, CEO at platform for supply chain payments Tradeshift, an overhaul of the whole landscape is required.
“I honestly think we need to put manufacturing far away from home to bed for good as it has had a horrible impact on the world," he says. "Shipping goods all over the world came with a massive carbon footprint, not to mention the damage it has done to labour costs being pushed to [very low levels].
“Resilience needs to be a consideration across the board, economically, sustainably, ecologically and politically. The good news is that we have the technology to make this shift happen now, to build more regional manufacturing hubs that use rails rather than trucks, for instance. It is paramount to decentralise.”
Lanng explains how the old supply chain model was built around a post-war world that was stable and predictable. That world no longer exists and adaptability is now more important than ever.
“We are looking at a prolonged period of instability, so the question is how do we transition from a system that is very stable and static to one that is very dynamic and changes constantly?” he asks.
Resetting costumers’ expectations could be a start. “Do we actually need constant deliveries from Amazon?" Lanng adds. "We have been taking delivery expectations too far. Maybe it is ok to wait a few days for something to be delivered to you."
As usual with complex issues, the solution is multifaceted and meaningful change takes time. “It is not easy as we are facing myriad different situations,” says Douglas Kent, executive vice-president of strategy and alliances at the Association for Supply Chain Management.
“Some recent studies have highlighted the importance of gaining additional visibility in the multi-hierarchy in supply chains in order to have a control tower viewpoint before disruption even occurs," he adds. "There is certainly more visibility now both upstream and downstream in supply chains to mitigate disruption.
“Having tighter and more strategic relationships with distributors and seeing them as partners rather than vendors also helps, and finally, having a playbook to refer to in order to not simply react on the spot when a disruptive event occurs is also key.”
In the US, companies have been assessing different options to address their delivery route issues.
“Companies are evaluating their current shipping lanes to determine whether their concentration or reliance on a few ports – export or import – is a ‘safe’ model going forward," says Page at Page Fura.
“Secondary ports will likely pick up additional business to the extent they can handle the current crop of ocean-going vessels.
"Although we are not total believers in the nearshoring or reshoring phenomenon, there is no question that at least some relocation of manufacturing/sourcing is occurring, particularly in those sectors or industries where there has been a disproportionately high concentration within a single country. The experience of companies in confronting semiconductor shortages is just one example of an industry that is currently undergoing upheaval."
The importance of talent
Over the past two years, the supply chain industry in the US has had time to reflect, do its homework and come up with a new solutions and models to alleviate its problems.
The new criteria mainly include nearshoring or reshoring production, diversifying suppliers and building inventories at critical points of the supply chain.
The latter is a solution that many companies have adopted as a way to quickly address the crisis. However, it is not a sustainable one.
“Building more inventory points is a very topical issue at the moment," says Kent. "For many companies, that was the answer to mitigate risk and create more stocking points. However, it is expensive and risky.”
The problem with creating more inventory is that it essentially creates more demand on the supply chain and does not push suppliers to absorb costs. “On top of that, payments get deferred, so a 20% dial up on inventories is a 100% dial up on inflation,” adds Lanng.
A more holistic rethink of the whole supply chain system is needed, one that focuses on creating a better flow so that containers in US ports are not left uncollected on the docks, and one that tries to increase the much-needed capability of a system that now very much depends on sea shipments.
Another factor, however, is increasingly being seen as crucial in establishing who the winners and the losers of the supply chain industry are going to be in the future, and that factor is talent.
“Workforce development is absolutely essential to secure the future of healthy and reliable supply chains in future,” says Kent.
“The industry really needs to make an effort at making warehousing and logistics jobs more attractive and turning them into a career choice rather than just a job. A supply chain worker learns many skills that are transferable to other professions, such as understanding inventory and gaining optimisation techniques.”
While conversations within the industry seem promising when it comes to getting logistics back on the right track, actions must follow, along with an acceptance that this will not be a smooth and fast path.
“I don’t think the situation is going to be a lot better in 2022, and not even in 2023," says Lanng. "We are going to see continuous change. However, the industry needs to adapt. If anyone is trying to hold their breadth until it all goes back to normal, they are going to run out of air.”
Supply chains have made the headlines as never before in the past two years due to the challenges they have faced as a result of the Covid-19 pandemic. The volatility they are experiencing is unlikely to go away any time soon, but the world is thinking about the way it moves goods in a very different way, and that will hopefully mean that it will be better prepared for the next pandemic or black swan event.