
The energy transition is driving a huge surge in demand for aluminium, but the industry is facing huge capacity constraints because of the big hike in energy costs in 2022.
Aluminium is both an important input to a number of technologies critical to the energy transition and a major source of carbon emissions, responsible for around 3% of the world’s direct industrial emissions in 2021, according to the International Energy Agency (IEA). Alumina refining and aluminium smelting are responsible for more than 90% of aluminium production’s direct carbon gas emissions.
The global consumption of aluminium semi-finished products is forecast to grow by 33.3 million metric tonnes (mt) in the following decade to 119.5mt in 2030 from 86.2mt in 2020, according to CRU Consulting. It is expected that global demand will increase to 179mt per year by 2050. Semi-finished products are all those ‘intermediate’ goods that underwent a first industrial process but require additional processing to define their final use. Around 37% of this growth is expected to come from China, followed by 26% from Asia (excluding China), 15% from North America and 14% from Europe. Global aluminium production saw average annual growth of 6% in the period between 2010 and 2018.
The highest growth in terms of absolute demand will come from the transportation sector, driven by decarbonisation policies and the shift from vehicles powered by traditional fossil fuels to electric vehicles (EVs), according to CRU Consulting. It will go from consuming 19.9mt of aluminium in 2020 to consuming 31.7mt in 2030. Most of this growth will come from China (33%), North America (22%) and Europe (19%).
By 2026, aluminium content per vehicle will rise by 12% to meet the needs of future hybrid vehicles and EVs, according to the Aluminium Association, an industry body. Light trucks such as the Ford F-150 Lightning are expected to have an average of almost 225kg of aluminium content. Luxury sedans such as the Tesla Model S and sports cars like the Acura NSX will have more than 360kg of aluminium content.
In 2021, Volkswagen said that aluminium makes up 126kg of a typical 400kg electric car battery, more by far than any other metal. The International Aluminium Institute (IAI), an industry group, forecasts that aluminium’s usage in batteries and other EV components means that automobile manufacturers will double their aluminium consumption by 2050.
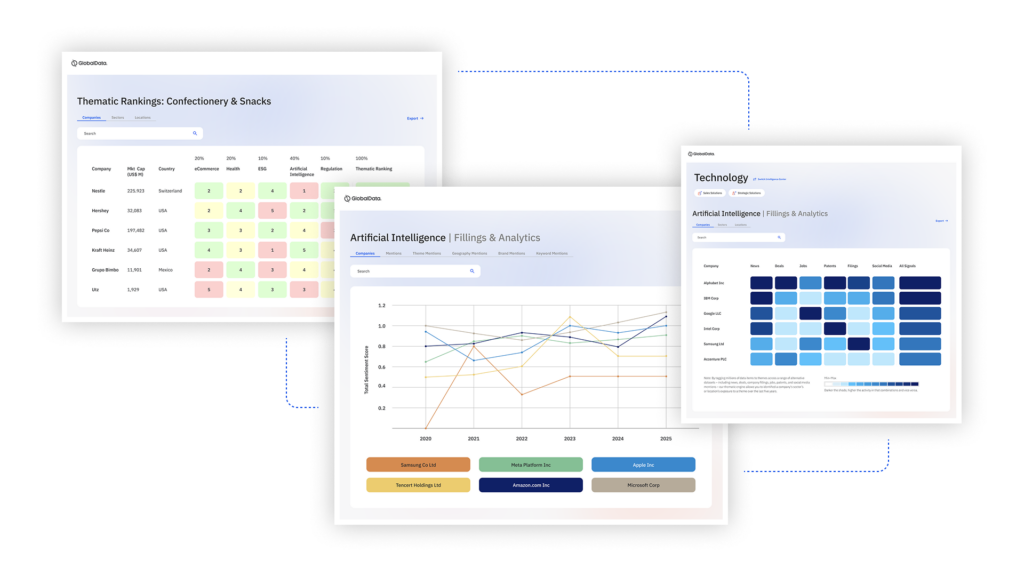
US Tariffs are shifting - will you react or anticipate?
Don’t let policy changes catch you off guard. Stay proactive with real-time data and expert analysis.
By GlobalDataPower grids will require a lot more aluminium in the future
In the electrical sector, the transition towards green energy sources will strengthen demand for aluminium, which will reach 15.6mt in 2030, starting from 10.4mt in 2020. China is expected to account for 47% of this growth.
The electrical sector represents one of the greatest opportunities for the aluminium industry in coming years as countries transition to renewable energies – which are more intensive in their use of aluminium than traditional energy sources – and expand their power grids. Solar power requires more than four times more aluminium per installed megawatt than wind power and about 25 times more than coal.
The need for conductor cables for power distribution will also increase. Although they have been traditionally made from copper, aluminium is a cheaper alternative. It is lighter than copper but requires more material to be used to achieve the same electrical conductivity.
Furthermore, aluminium consumption from the packaging sector is expected to jump to 10.5mt in 2030 from 7.2mt in 2020, driven mainly by the rise in popularity of canned drinks in North America, Europe and China. This is strongly linked to the negative perception that Western consumers have of polyethylene terephthalate and other plastics that normally compete with aluminium in this space.
However, the aluminium value chain is facing myriad challenges and one of the biggest is where all the increased smelting capacity will come from. During the past two decades, China has built up a massive smelting capacity, but, in 2017, the government put in place a capacity ceiling of 45mt of aluminium production a year. It has been enforcing a strict old-for-new policy in the aluminium sector – new smelters have only been permitted when matching older capacity is closed.
Electricity used during aluminium smelting accounts for more than 60% of the aluminium industry’s carbon emissions, according to Accenture. In October 2020, President Xi Jinping pledged that China would reach peak carbon emissions before 2030 and become carbon neutral by 2060. That is a big ask for the country’s aluminium sector, which, in 2018, was 90% reliant on coal power to energise its potlines.
Aluminium smelters are power hungry
This could create a window of opportunity for producers elsewhere in the world, but aluminium smelters are power-hungry plants and the rise in electricity prices in 2022 has hamstrung the aluminium smelting industry in the developed world. One metric tonne of aluminium takes about 14,000 kilowatt-hours to produce, enough to supply electricity to the average UK home for almost five years. German power prices for 2023, a benchmark for Europe, soared to €543 per megawatt-hour in August 2022, 12 times higher than two years before (the price was back down at €155 on 16 October 2022 but still much higher than previously).
Energy costs account for 40% of total primary aluminium production costs normally, according to European Aluminium, an industry body. This year they would have gone up significantly. Aluminium production requires around 40% more energy than copper, for example.
Experts say it is a paradox that aluminium production is being hobbled by the very sector – electricity – which needs it most for decarbonisation – whether it be directly in the form of solar panels or indirectly in the lightweighting of EVs.
Around 1.1mt – amounting to 50% of the EU's aluminium production capacity – has already been forced offline during 2022 due to the power crisis, according to Eurometaux, an industry body. This year, a number of European smelters have had to close and European aluminium production now sits at its lowest level since the 1970s. In October 2021, the Dutch aluminium producer Delfzijl Aluminium, popularly known as Aldel, stopped annual production capacity of 110,000 tonnes (t) due to high electricity prices.
In September 2022, Norsk Hydro shuttered a smelter in Slovakia while Aluminium Dunkerque Industries France, Europe’s largest aluminum smelter, reduced its production by 22% in October 2022. There has also been a 33% curtailment at Alcoa's Lista smelter in Norway, a 59% production cut at Speira's Rheinwerk smelter in Germany and reduced output at Alcoa's San Ciprian alumina refinery in Spain. Norsk Hydro also decided to keep smelting pots at its Husnes and Karmoey plants in Norway offline after normal maintenance. Alro's alumina facility in Romania was also shut down.
These closures run counter to the EU’s goal of strengthening the domestic processing of strategic minerals – with the bloc’s latest list including bauxite, the ore used to produce aluminium. Industry figures say the closures would also knock global efforts to slash carbon gas emissions because European smelters generate three times less than those in China, where coal is often used to generate electricity.
China’s aluminium production holds up
China’s aluminium output has held up despite the energy crunch. Its primary aluminium production hit a record in August 2022, surging 9.6% year-on-year to 3.51mt, according to the country’s National Bureau of Statistics. Output in the first eight months of the year grew by 2.1% to 26.47mt. In China, coal is cheap and many power plants and smelters are owned by local governments that have a big interest in maintaining output even if it does not make sense economically.
In October 2022, the Biden administration also said it was considering restricting imports of Russian aluminium as it charts possible responses to Moscow’s recent military escalation in Ukraine. The Russian company Rusal is the world’s largest aluminium producer outside China. Rusal’s annual production capacity is about 4.5mt, accounting for 6% of the total global aluminium capacity and 13% when excluding China. Rusal is the largest supplier of aluminium in Europe, with 40% of its production destined for Europe.
“We think there is a very positive outlook for aluminium,” says Miles Prosser, the IAI’s secretary-general. “It is lightweight, abundant in the Earth’s crust, a very workable material, durable and conducts electricity. These characteristics are helping to drive aluminium demand in some of its key markets. It has qualities that people are interested in when they look to do things more sustainably.
“The aluminium content in an electric vehicle is higher than that in a conventional vehicle, for example. We were expecting quite strong growth in demand from the automotive sector anyway but, the more that there is a trend towards electric vehicles, the greater the growth. Another important driver is electricity generation and infrastructure. There is a big push all around the world to move away from conventional energy sources to renewable ones. That does two things: first, you must put in those new energy sources; for example, solar panels use aluminium.
"Second, new investment in infrastructure, in the power grids. The drive to build up new energy sources means you must invest in the grid to connect up those new energy sources. Some of the new sources such as solar and wind are intermittent, so you must build larger generation capacity in order to be able to meet demand and you have to build larger networks in order to be able to supply from a range of sources.”
The world has enough bauxite for up to 340 years
Aluminium production starts with the raw material bauxite, a mineral found mostly in a belt around the equator. Bauxite is the only ore that is used for commercial extraction of aluminium today. Four tonnes of it are needed to make a single tonne of aluminium. Global bauxite resources are estimated to be 55–75 billion tonnes (bt), and at the current rate of extraction, these reserves will last 250 to 340 years. The majority of the global bauxite reserves can be found in Australia and Africa.
Aluminium oxide – alumina – is extracted from bauxite in a refinery. Alumina is then used to produce primary aluminium through the smelting process. The production of primary aluminium takes place in large production lines. Primary aluminium is alloyed with other elements such as copper, manganese and silicon for additional strength, corrosion resistance and other properties. These are then cast into billets, remelt ingots, slabs and rods and other castings for further processing.
The world’s stock of aluminium in use is like a resource bank. Around 75% of the aluminium ever produced is still in use and some of it has been through countless recycle loops.
Since China announced its cap on aluminium production capacity, the Middle East has become a much bigger player in the smelting industry. The Middle Eastern countries – including the United Arab Emirates, Bahrain, Qatar, Oman and Saudi Arabia – with access to cheap gas are looking to develop their broader economies, and smelting is playing a significant role. The energy-intensive nature of producing aluminium means that parts of the world with low-cost hydroelectric power or natural gas have an advantage.
“Aluminium can be a way of converting competitive electricity into a tradeable commodity,” adds Prosser. “If a country has electricity, it is difficult to sell it because it needs cables and wires to sell it elsewhere in the world. However, with aluminium you can convert that electricity into a physical product that can be traded around the world.”
Middle Eastern countries are now considering options for how they decarbonise the electricity used in smelting – so-called 'green aluminium' – and are investing in solar, wind and nuclear.
Alumina refining is dependent on the availability of bauxite and energy in the form of heat (normally in the form of coal or gas to provide the high temperatures needed for processing bauxite). In monetary terms, alumina is worth at least ten times the value of raw bauxite. This sector also wants to decarbonise, but it is a much harder process because energy in the form of heat is required.
China is an important alumina-refining country but countries that have access to bauxite reserves are also significant, including Australia, Brazil and Indonesia. Africa has great potential, but at the moment there is limited alumina refining on the continent.
Guinea has world’s biggest bauxite reserves
Meanwhile, in 2021, Australia was the biggest producer of bauxite worldwide (110mt), followed by China (86mt) and Guinea (85mt), the small west African country. Brazil, India and Indonesia are also important bauxite-producing countries. Guinea has the world’s biggest bauxite reserves, with an estimated bauxite ore reserve of 7.4bt, mostly concentrated in the western and central part of the country. It is followed by Australia at 6.2bt and Brazil at 2.6bt, according to the US Geological Survey.
There are significant environmental issues at every key stage of the aluminium value chain. Bauxite mining takes place at the surface, quarries can cover large physical areas and there is no way to do the mining without removing the overlying vegetation.
Bauxite mining is the biggest contributor to deforestation within mining leases in the Brazilian Amazon rainforest and has led to widespread loss and destruction of agricultural land and water resources in Guinea, according to GermanWatch, a non-governmental organisation. At least 14 Chinese companies have mining-related operations in Guinea.
The mining often happens near farms and residential areas because bauxite-bearing soil can also be fertile. When land is cleared, dust can spread in air and water as wind picks up particles from mines and trucks travelling with ore.
In early 2016, the Malaysian government banned all bauxite mining after unregulated mining and run-offs from unsecured stockpiles in the eastern state of Pahang contaminated water sources, turning roads, rivers and coastal waters red. The government ended the moratorium on bauxite mining in 2019.
The forests and farms of Indonesian Borneo are also cratered with waterlogged pits left behind from the boom years of bauxite mining. These old mines remain open to the elements, allowing heavy metals in the soil to be dispersed into the air and waterways. Unless top soil is replaced, the land cannot be used for farming.
“Removal of vegetation for bauxite mining is an almost unavoidable fact,” says Prosser. “However, it is a short-lived removal of the vegetation before you are then in a position where you can start rehabilitating. We are talking about rehabilitation after the first year’s operation. Government capacity for regulation is a key part of getting rehabilitation to occur, but the other contributor is the values and practices that the companies bring to that operation, so in somewhere such as Guinea you have a variety of operators. Some of those companies are operating elsewhere in the world – for example, in Brazil and Australia – and have strong regulatory regimes and excellent practices. They are bringing those practices into Guinea.”
Alumina refining generates 120mt of red sludge globally
Alumina refining can also cause severe environmental damage. For roughly every tonne of alumina, two to three tonnes of waste – called ‘red mud’ – is created. It is very difficult to control and to prevent from contaminating nearby water bodies. About 120mt of this highly alkaline red sludge – containing iron, titanium and silicon oxides – is produced worldwide each year. Due to its high basicity and potential leaching, its storage is a critical environmental problem. The material is typically stored in dams, which require prior care of the disposal area, and needs monitoring and maintenance throughout its useful life.
Australia is one of the countries in the world that benefits the most economically from the aluminium value chain. It is the world’s largest producer of bauxite and second-largest producer of alumina. The bauxite, alumina and aluminium industries contribute around A$15.9bn ($10.05bn) a year to the economy in export value, according to the Australian Aluminium Council (AAC). More than A$14bn of this comes from the alumina and aluminium industries, as value-adding mineral processing sectors. Australia is the world’s largest exporter of alumina and aluminium is Australia’s highest-earning manufacturing export.
The country mines more than 100mt of bauxite a year, or about one-quarter of global production. About 40% of this is exported and the remainder is turned into alumina in Australia. The country is the world’s second-largest producer of alumina, producing about 20mt a year.
“Meeting the continued and increasing global demand for primary aluminium will require proportionate increases in production of bauxite and alumina,” says Marghanita Johnson, AAC’s chief executive officer. “Australia is well-positioned to continue to supply global markets. It has the systems and processes to extract and process critical minerals such as bauxite into alumina and into aluminium safely, efficiently and sustainably.
“With decarbonisation of Australia’s electricity supply being the single biggest opportunity to decarbonise the vertically integrated industry, it is important to consider the role Australia’s grid-connected mines, refineries and particularly smelters perform in grid stabilisation, which helps with increased penetration of variable renewable electricity.”
She adds that the carbon intensity of the Australian grid is declining rapidly with this increased penetration of variable renewables. Furthermore, the aluminium industry has the opportunity – as part of contract renewal – to source firmed renewable electricity from on-grid sources or behind-the-meter sources. One of the industry’s biggest challenges is long-term storage at scale, which can address periods when there is both low solar and low wind output (dunkelflaute). This is beyond the current storage term of pumped hydro, batteries and transmission solutions.
Johnson also says that the country has an opportunity to leverage the clustering of skills, resources and energy demand in the regions in which aluminium smelters and alumina refineries are located.
“Strengthening our national manufacturing capabilities will put Australia in the strongest possible position to meet these future forecasts for not only traditional commodities such as bauxite, alumina and aluminium, but also other emerging aluminium-related commodities such as high purity alumina, aluminium alloys and aluminium salts,” she adds.
Despite the aluminium industry’s supply constraints in 2022, aluminium prices have been on a mostly downward trend since the start of the year because of the economic downturn and property crisis in China, as well as concerns about a recession globally. On the London Metal Exchange (LME), the aluminium price ranged between $2,150 and $2,200 per tonne in mid-October 2022. It briefly touched a high of $3,877.50 in March 2022. LME analysts predict aluminium prices of $2,600–2,650/t in the financial year 2023–24.
The aluminium value chain is vital to the energy transition but throws up a lot of challenges for Western countries. China is a significant player in aluminium smelting and alumina refining. It also owns or controls bauxite mines around the world. This could present a geopolitical risk in the future as the developed world finds it increasingly hard to produce its own aluminium due to high energy costs. Furthermore, environmental issues surround the whole value chain, which the industry will be grappling with for many years to come.