
Industry 4.0 is dramatically transforming the global pharmaceuticals supply chain after severe disruption after the Covid-19 pandemic, with the effects still felt on the pharmaceutical industry.
The pandemic affected most aspects of biopharma’s global value chain, from sourcing raw materials to distributing finished products. With a big proportion of the global population in quarantine, plant closures and supply shortages across the extended supply network led to significant global supply chain disruption. By May 2020, 85 countries had enacted pandemic-related trade restrictions. The bans have now been lifted but global pharma supply chains have changed forever.
As if the pandemic were not enough, the Ukraine crisis has had a profound impact on the global pharma value chain, as well. The pandemic and the conflict combined have prompted a big increase in raw material and fuel costs. Drug shortages and supply chain security have become one of the most significant issues for the pharma industry worldwide.
Manufacturing locations affecting supply movements
An active pharmaceutical ingredient (API) is the component of an over-the-counter or prescription medication that produces its intended health effects. GlobalData’s Pharmaceutical Sourcing and Onshoring Report (2022 edition) surveyed 105 pharma clients and prospects from around the world between 26 May and 17 June 2022. It showed that 72% of the United States Food and Drug Administration-approved API facilities were abroad while 66% of the European Medicines Agency-approved APIs were made in the Asia-Pacific (APAC) region. The survey asked respondents whether they would address supply chain risks by moving manufacturing closer to home or diversify with more foreign suppliers.
Some 72% of correspondents from North America indicated that they would maintain the same balance, while 6% said that they would shift a greater proportion of API manufacturing abroad, away from their headquarter country or main countries where they operate. But 22% said that they would shift a greater proportion of API manufacturing to their headquarter country (known as onshoring) or to the main countries where they operate or where their clients operate.
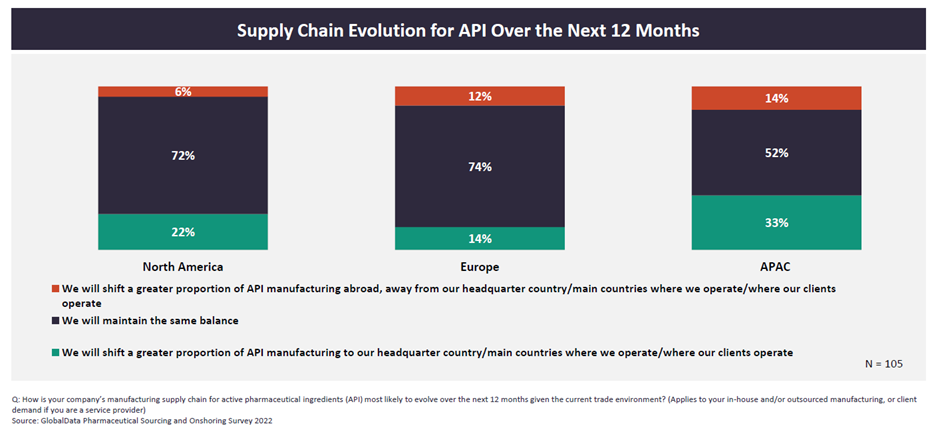
Meanwhile, among correspondents from Europe, 14% said that they would shift a greater proportion of API manufacturing home or to the main countries where they operate, 74% said they would maintain the current balance, and 12% said they would shift a greater proportion abroad. Correspondents from the APAC region were the most likely to shift manufacturing closer to home or to the main countries where they operate — 33% indicated that they would do that. Meanwhile, 52% said they would maintain the current balance and 14% said they would shift a greater proportion of API manufacturing abroad.
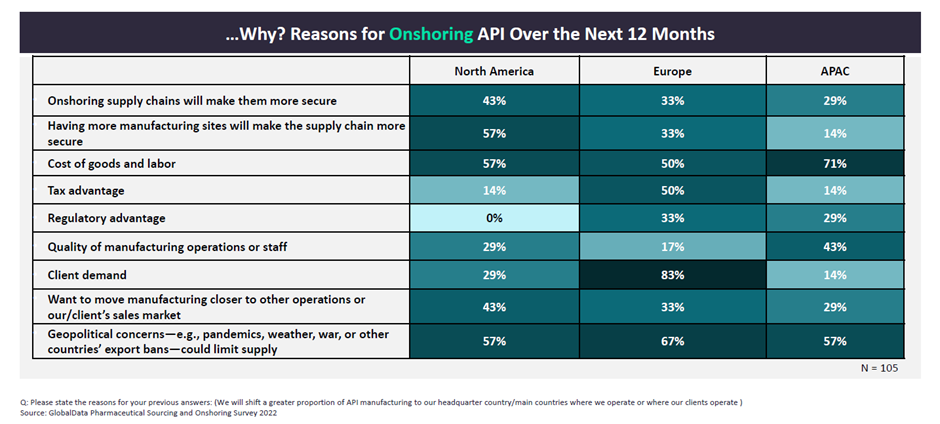
However, at the same time as pharma companies are changing their supply chain for security reasons, another transformation is under way — Industry 4.0. It conceptualises the rapid transformation of technology, industries, and societal patterns and processes in the 21st Century on the back of increasing inter-connectivity and smart automation. It relates to the trend towards automation and data exchange in manufacturing technologies and processes, including cyber-physical systems (CPS), Internet of Things (IoT), industrial internet of things, machine learning, cloud computing, cognitive computing and artificial intelligence.
Pharmaceutical firms are changing the way they do business. The future industry leaders will be highly automated and digitalised. IoT devices can monitor shipments from vial to patient, while artificial intelligence (AI) and machine learning are making once laborious processes faster and more efficient than ever before, saving time and labour costs.
IoT in the cold chain
For example, IoT is transforming the global pharma cold chain industry, whose value is estimated $73bn a year. To ensure temperature-critical medicines, such as vaccines, are fit for purpose, cold chains must be carefully monitored and products tracked throughout the entire journey from manufacturer to patient. Some companies are already embedding IoT temperature sensors within individual cartons, creating an effective audit trail. Applications are also being developed that will use machine learning to generate predictive data on environmental hazards in the biopharma cold chain cycle.
DP World’s cold chain facilities — for example, those in Caucedo port, the newest and most modern port in the Dominican Republic — span warehousing space and moving goods vehicles. They ensure that DP World can cover the entire journey from the warehouse to the laboratory. In the Dominican Republic, this meant distributing more than 8 million Covid-19 vaccines throughout the country.
DP World’s suite of digital technologies — including CARGOES Flow — is also helping its partners identify bottlenecks in their supply chains and smooth the flow of medical supplies across borders. Furthermore, the DP World Digital Freight Alliance is an online network primarily designed to provide freight forwarders with new tools, routes and services, therefore enabling them to do more business. Membership in the alliance grants access to freight forwarders in more than 150 countries, proven and reliable logistics partners through the KYC process, increased sales, payment protection and many other features.
AI has the potential to address some of the biggest challenges in pharmaceutical cold chain management. Most companies capture only a fraction of their data’s potential value. By aggregating and analysing data from multiple sources — a drug order and weather data along a delivery route, for example — AI-based systems can provide complete visibility with predictive data throughout the cold chain. Before the cold chain starts, suppliers can predict hurdles and properly allocate resources.
Analytical decision-making relies on companies having actionable data and real-time visibility throughout the cold chain. Just-in-time delivery of uncompromised drug product relies on predictive data analytics. Patient risk and gaps in the pharmaceutical pipeline will be substantially reduced through the use of analytical decision-making.
Increasing agility
Pharmaceutical supply chains are characterised by a severe lack of agility. Studies show that the replenishment time from manufacturer to distribution centres average 75 days in the pharma sector compared with 30 days for other industries. The true value of AI lies in improving the pharma value chain’s agility through assuring drug efficacy, patient identity and the chain of custody (the system of controls governing the collection, processing and storage of samples).
For example, DataRobot is a machine learning platform for automating, assuring and accelerating predictive analytics. Its open-source algorithms are able to model automation by using historical drug delivery data. Supply chain managers can build a model that accurately predicts whether a given drug order could be consolidated with another upcoming order to the same location or department.
Furthermore, biomarkers are naturally occurring molecules, genes or characteristics by which a particular pathological or physiological process or disease can be identified. They are making personalised medicine mainstream. However, they mean that pharma companies must stock many more therapeutics, but in much lower quantities. AI-based inventory management can determine which product is most likely to be needed (and how frequently), track exactly when it is delivered to a patient, provide the delivery time and monitor any delays or incidents (they could trigger a replacement shipment within hours).
In the case of personalised medicine, DP World says the demand is increasingly oriented towards smaller quantities of high-value goods delivered to meet timelines and conditions that are significantly more challenging. With medical goods that have strict temperature requirements, a fluctuation as minor as 2 degrees Celsius can reduce or even eliminate effectiveness.
Meeting shifting demands
For decades infrastructure has moved towards larger vessels and is not set up to meet the shift in demand. Fleets of smaller ships designed for speed and more specific quantities are needed. DP World’s Unifeeder and FeederTech acquisitions are designed to stay ahead of the new trend, optimising speed and response for shorter supply chains, while also serving as key spokes in larger blue sea operations. Booking and tracking reefer capacity within this network adds an additional level of capability, one of the keys to success in the medical supply chain.
Complex processes, across a number of locations, all depend on logistics working in a synchronised way. GlobalData analysis shows that the journey of medicines and medical equipment — enabled by technologies such as big data analytics, blockchain and IoT sensors — is set to become more streamlined and secure. Creating and maintaining inventories of medical supplies — in particular on a global scale — could help to tackle pharmaceutical supply shortages, address quality control issues and prevent counterfeit products from entering supply chains.
Products can be tracked by linking purchase with transport orders and warehousing tracking data with in-transit telematics. Real-time tracking updates allow freight forwarders to use AI to find the best shipping routes, avoiding blockages and increasing efficiency and sustainability.
Blockchain is also expected to play an important role in logistics infrastructure in the future. It can be integrated to help provide earlier visibility of container flows across multiple carriers. DP World says this means that medical goods in transit can be monitored around the clock and cargo owners can plan for necessary intervention in the case of unexpected delays or temperature fluctuations.
Furthermore, when the acquisition of data is coupled with blockchain technology to manage the validation of goods, DP World thinks cargo owners will be better placed to order more accurately. They will also be able ship more quickly and do so more frequently. This shift in behaviour will reduce the amount of stock held in warehouses and wastage, lead to a significant increase in the speed that goods can get from origin to destination and enable the greater personalisation of goods.
The global pharma supply chain has experienced a perfect storm during the past few years. The pandemic and Ukraine crisis upended traditional supply chains. Onshoring is becoming a lot more common. However, some of the biggest changes for the supply chain are still to come and relate to Industry 4.0.