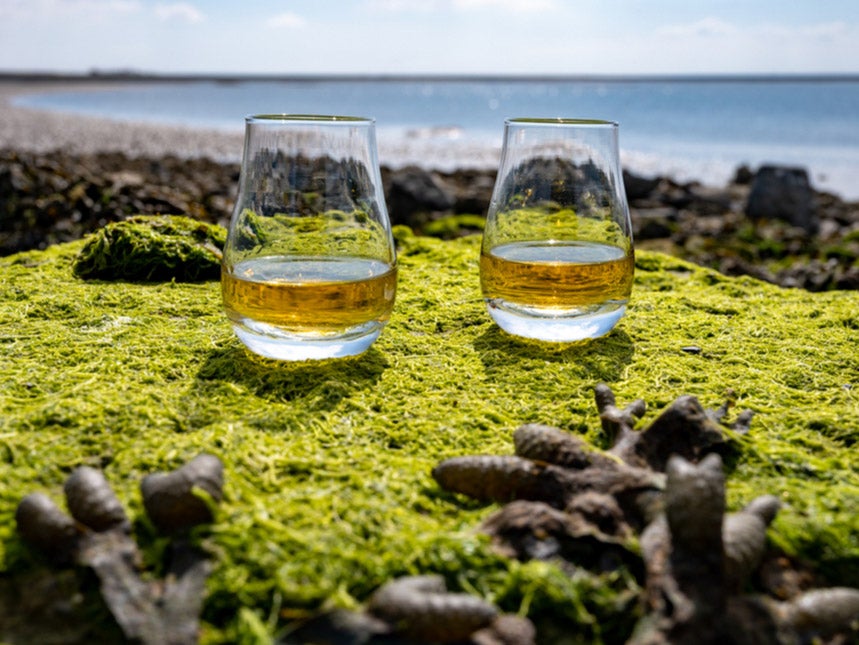
The whisky industry is a major contributor to the Scottish economy and is making progress to reduce its carbon footprint – with hydrogen a potentially key solution.
In 2022, Scotch whisky accounted for 77% of Scottish food and drink exports, worth £6.2bn ($7.77bn) and accounting for more than 25% of total UK food and drink exports. The industry is worth an estimated 4.9% of the Scottish economy.
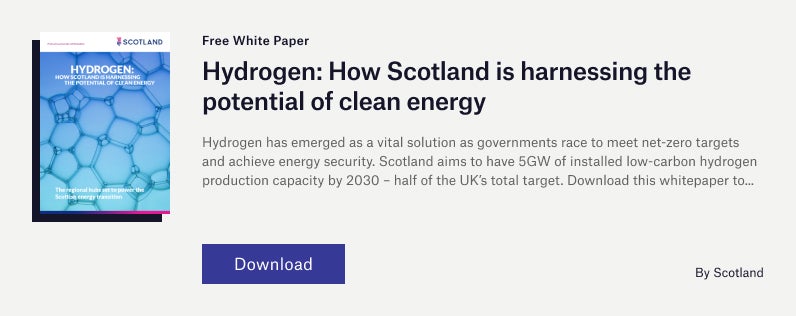
However, the economic benefits must be balanced with an awareness of the industry’s environmental impact. Scotland’s 148 distilleries consume 3.7 terawatt-hours (TWh) of energy a year, according to figures from Energy Voice, with 140 gigawatt-hours (GWh) from electricity demand.
Despite several distilleries transitioning to less carbon-intensive fuels such as liquid petroleum gas (LPG) or compressed natural gas (CNG), these cannot be considered long-term solutions to reach net zero. Attention is now turning to hydrogen, which emits no carbon when used. While current industrial hydrogen production methods are carbon-heavy, it can also be produced in a zero-emissions way using an electrolyser powered by renewable energy to split water into its chemical elements.
In Scotland, distilleries seeking to use hydrogen to power processes can tap into a wealth of expertise in this emerging clean and low-carbon energy sector. Hydrogen is integral to Scotland’s plans to reach net zero by 2045. As soon as 2030, there is an ambition to have 5GW of production capacity for hydrogen using renewables or low-carbon processes. This capacity increases to 25GW by 2045.
With costs being one of the key barriers to using hydrogen for industrial processes, the sheer volume of projects in planning in Scotland could see prices fall.
Decarbonising distilleries with hydrogen
The Scotch whisky industry has announced ambitions to achieve net-zero emissions by 2040, five years ahead of Scotland’s national target and a decade ahead of the wider UK’s goal. As a zero-emission energy source at the point of use, hydrogen could play a key role in achieving these targets, especially for distilleries in remote areas that are not connected to the natural gas network.
The UK Government has allocated funding for a series of projects to use hydrogen to power Scottish distilleries. One of these is Project WhiskHy being developed by a consortium headed by Supercritical – a UK-based innovator in clean energy technologies. The company is developing a high-pressure electrolyser, which it claims will reduce the costs of pressurised hydrogen while delivering high levels of efficiency, also saving electricity and significant floor space required for storing the energy source.
Project WhiskHy involves two of the five Scottish distilleries owned by Beam Suntory, the globally renowned spirits producer. The spirits company has committed to halving emissions by 2030 and sees hydrogen as a potential solution.
Beam Suntory became involved in the project after a call from Scottish Enterprise, Scotland’s national economic development agency – which also commissioned an extensive research study titled Hydrogen for Scottish Distilleries, published in June, detailing the scale of the projects under way.
“Scottish Enterprise is really engaged and focused in trying to deliver projects and provide the opportunity for businesses to really push the boundaries of what is possible,” explains Alistair Leckenby, environmental and sustainability manager at Beam Suntory.
Scaling up of green hydrogen projects at distilleries
In phase one of Project WhiskHy, Beam Suntory’s Ardmore Distillery in Huntly, Aberdeenshire, was the focus of a study investigating the technology’s feasibility for producing hydrogen from wastewater at the site. This could significantly decrease the amount of freshwater needed by electrolysers for hydrogen. After successfully securing £2.94m in funding from the UK Department for Business and Trade, phase two will see the scale-up of the electrolyser and an industrial hydrogen trial initially planned at Beam Suntory’s Glen Garioch Distillery, approximately 18 miles east of Ardmore Distillery.
The Supercritical technology could bring back the traditional process of direct firing to more distilleries.
More intense levels of heat create Maillard reactions, which Leckenby says unleash a greater depth of character flavours in the distillate, due to the increased chemical reactions.
Due to the historically high carbon impact, many distilleries have moved away from direct firing to use indirect heating instead. However, the temperatures achievable for indirect heating are far lower than direct firing.
“You have a big steam boiler, steam pans, and you are using steam to boil the liquid, but the steam temperature might be 130°C [with indirect heating],” adds Leckenby. “Whereas the temperature you can potentially get from direct firing at the interface between your heating source and your liquid inside the pot, the difference can be up to 1,000°C.”
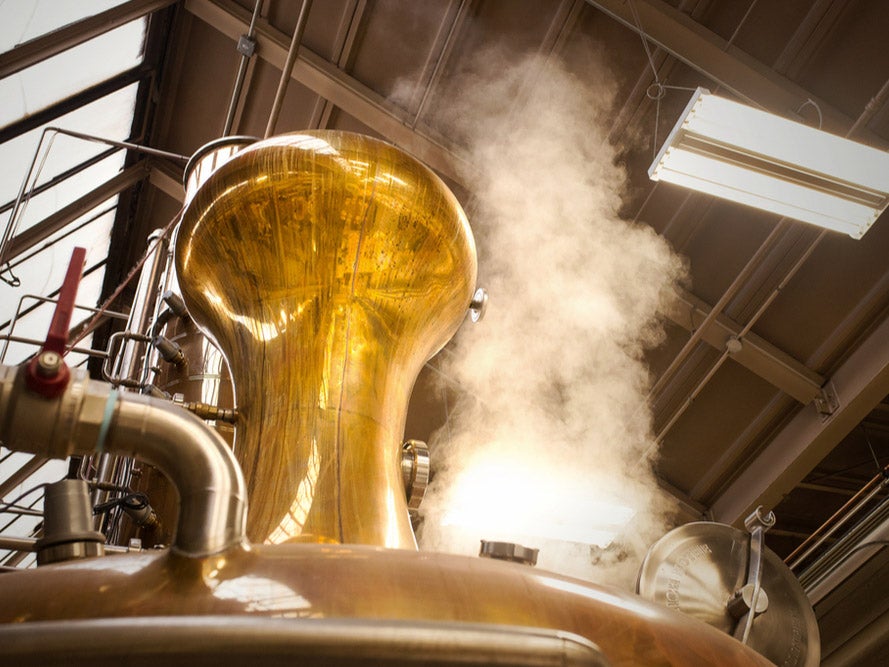
New technologies for traditional distillery processes
A couple of years ago, as part of a wider distillery refurbishment project, Glen Garioch reintroduced direct firing in the wash still, the first step of the distilling process, currently powered by methane. Beam Suntory believes that direct firing contributes to significantly improving the flavour of the whisky.
“Our business belief is that more traditional production methods of whisky produce a greater richness and depth of character in the spirit – ultimately producing, after maturation, a product with elevated quality, character, flavour and composition.”
Hydrogen will be trialled as a replacement for methane in direct-fired distillation during phase two of trials in Project WhiskHy, expected to start in the first quarter of 2024. Leckenby suggests the higher temperatures possible from hydrogen offer a key advantage.
“We are looking to determine that if you could replace that methane with hydrogen and use hydrogen to direct-fire, we will hopefully maintain the elevated level of quality that we have achieved – but hydrogen can actually burn hotter,” he says. “So, we might be able to further increase the intensity of the conditions underneath the pot by using hydrogen. My hope is that we can further enhance that richness and depth of character.”
Developing distilleries powered by zero-emission energy while improving product quality is integral to Beam Suntory’s Proof Positive strategy, which is aimed at delivering sustainable changes for operations that benefit nature, consumers and communities.
“If we can use hydrogen to elevate the quality of our spirit and then in the future use a net-zero source of hydrogen, then it is a fantastic way of producing Scotch using traditional methods and techniques in the 21st century without carbon consequence,” adds Leckenby.
Scottish distilleries going green
Several other feasibility studies have been carried out or are under way to explore how hydrogen can be used in whisky manufacturing processes across Scotland.
South of Aberdeen on Scotland’s east coast, the Arbikie Distillery’s hydrogen energy system is under way with support from Scottish Enterprise. The addition of a new 1MW wind turbine will supply renewable energy to power an electrolyser to produce hydrogen from water on site. A hydrogen-compatible boiler will power the distillery. Led by Scottish companies Locogen and Logan Energy, the project has secured phase one and phase two funding from the UK Government scheme.
Bruichladdich Distillery Project HyLaddie also secured phase one and two funding from the UK Government scheme. Located on the Isle of Islay off the Scottish west coast, the project will use grid electricity to power electrolysis, with the resulting hydrogen fed into a specially equipped boiler.
Meanwhile, InchDairnie Distillery in Fife received phase one funding through the UK scheme and is progressing with a project to use heat from a hydrogen boiler for its processes. The feasibility study has been looking into using hydrogen produced on-site from electrolysers or provided by large-scale producers nearby.
Another initiative is the HySpirits 2 project in Orkney. The project secured phase one funding and is being led by the European Marine Energy Centre in a partnership between Edinburgh Napier University, Edrington and Orkney Distilling.
Dual fuel technology was identified as the most effective solution, providing fuel flexibility as hydrogen production scales up to meet the demand. In the next phase, a dual fuel steam boiler will be deployed at Orkney Distilling for further testing to determine real-world performance. Orkney has considerable experience in green hydrogen, which is already powering several buildings on the islands.
For distilleries seeking hydrogen boilers, a key supplier could be Cochran Boilers. The Scottish company is experienced in providing fossil fuel boilers for the distilling sector and is now developing a hydrogen-ready model.
Scaling up hydrogen to meet demand
Enabling hydrogen production at scale will be crucial to meet growing demand. Distilleries producing hydrogen from renewables on-site will be a significant development and should ultimately bring operating costs down. Some of these processes could also produce biogenic CO₂, demand for which is growing due to its use as a feedstock for the production of alternative fuels for heavy transportation.
Furthermore, the development of 13 low-carbon or renewable hydrogen hubs around Scotland, as highlighted in reports by Scottish Enterprise and GlobalData, will enable distilleries to access reliable supplies of the energy source if they cannot produce it on site. For example, distilleries in Cromarty Firth are currently exploring ways to work with the Cromarty Hydrogen Project, which is projected to have a daily green hydrogen production capacity of 20 tonnes as soon as 2025.
Led by a partnership between ScottishPower and Storegga, connecting the Cromarty Hydrogen Project with distilleries comes off the back of a positive feasibility study between whisky manufacturers based in the Cromarty area, including Whyte & Mackay, Diageo and Glenmorangie. Hydrogen produced from the Cromarty hub could also be used by local food producers, manufacturing facilities and for industrial heating.
To learn more about how Scotland’s hydrogen economy is developing and the 13 regional hubs, download the specially commissioned document below.