
Emission-free rocket launches are not a realistic prospect anytime soon, but a series of innovations in Scotland are proving that it is possible to get into orbit with a significantly decreased carbon footprint.
Two companies leading the race for the first vertical rocket launch in Scotland are Skyrora and Orbex. The two are reaching new heights in reducing the environmental impact of the space industry – with sustainability of fundamental importance to both companies.
Increasing sustainability of space sector operations
Headquartered in Edinburgh, Skyrora’s team have scrutinised every industrial facet of space industry operations to determine the most sustainable options. An example of this is its engine testing facilities. Instead of building new warehouses equipped with blast-proof walls and the carbon footprint of materials and construction, the Skyrora team adapted a quarry – which already had the robust walls.
The company is using cleaner fuels made from plastics that can’t be recycled, containing ultra-low levels of sulphates. While the carbon impact when the fuel is burned is similar to existing kerosene, Skyrora is working with the universities of Strathclyde, Edinburgh and St Andrews to research further emission reductions and create more sustainable options. These fuels could be equally useful in reducing the environmental impact of maritime vehicles.
Alongside this, the company is developing 3D-printed rockets for vertical launch, and even working on the Space Tug project, which aims to one day clean debris above Earth and service satellites in orbit.
“It would be great if we could have the first zero-carbon rocket launch from Scotland,” says Derek Harris, business operations manager at Skyrora.
The world’s first carbon-neutral spaceport
Orbex has its headquarters and production facilities in Forres, 25 miles north-east of Inverness. Rocket testing is taking place nearby at the former Royal Air Force (RAF) base in Kinloss.
The company’s CEO, Martin Coates, one of Orbex’s original founding investors, explains that sustainability was a priority from the beginning. Measures to protect the local environment and unique ecology have been integral to the company’s development.
In November 2022, the company won the contract to operate Sutherland Spaceport on the A’ Mhòine peninsula in the north of the Scottish mainland. Orbex’s ambition is to make the Sutherland facility the world’s first carbon-neutral spaceport. Plans include protecting local peatlands by constructing a ‘floating’ road to allow the peat to retain its original water balance and creating tunnels for water voles to pass underneath.
Sutherland Spaceport is intended to provide low-cost orbital launch services for small satellites using advanced, low-carbon, high-performance micro-launch vehicles. Estimates suggest that the spaceport could be worth £1bn ($1.26bn) to the Highlands and Islands economy across the next three decades.
Using greener fuels and materials for more sustainable rocket launches
With cleaner fuels key to making space launches more sustainable, Orbex uses bio-propane (BioLPG) made from waste residues and sustainably sourced materials. This fuel offers the same performance as liquefied petroleum gas (LPG) but with a much lower carbon footprint.
“Choosing bio-propane means not only is it a sustainably sourced fuel, it also doesn’t produce any soot,” explains Coates. “It offers some really interesting technical developments. When you chill it to -200°C, it doesn’t pump very well compared with other fuel sources. So, we’ve had to uprate the entire engine system.”
Additionally, almost the entire structure of the company’s Orbex Prime rocket is made from carbon fibre, which is both robust and lighter than aluminium. Using lightweight materials for rockets can significantly reduce the amount of fuel required for launches.
“We are doing things in carbon fibre and cryogenics that nobody has done before,” Coates says. “Studies by the University of Exeter demonstrate that a single launch of Orbex Prime will have a carbon footprint with up to 96% less carbon emissions than a comparable launch system using fossil fuels. We are also looking at the launch systems themselves, working with other universities on how we can improve what we do from an environmental point of view.”
3D-printing rockets in Scotland
What expands the possibilities for rockets is 3D printing, which can optimise material use and create unique combinations. Skyrora is developing 3D printing for rockets. Even metallic dust from processes can be captured and reused. Crucially, 3D printing can also reduce the cost of rockets, decreasing the need to transport units to other locations for machining.
“Previously, if you made an engine from scratch, you would have to take the chunk of metal and work on it,” says Harris. “Those engines may have to go up and down the country to Portsmouth or Plymouth to be machined and come back. That is a lot of internal journeys.
“Being able to print these parts in-house, with a machine that actually not only 3D-prints but also machines it at the same time, hugely cuts supply chain costs.”
To further research, Skyrora has received around £500,000 in funding from Innovate UK as part of a consortium called Made 3D. Funds will allow the company to test-print two different types of metallic alloys for rockets.
“That allows us to have part of the engine made from Inconel, so, it is strong, but then we can have an inside coating such as copper, which is much lighter with better heat properties,” comments Harris.
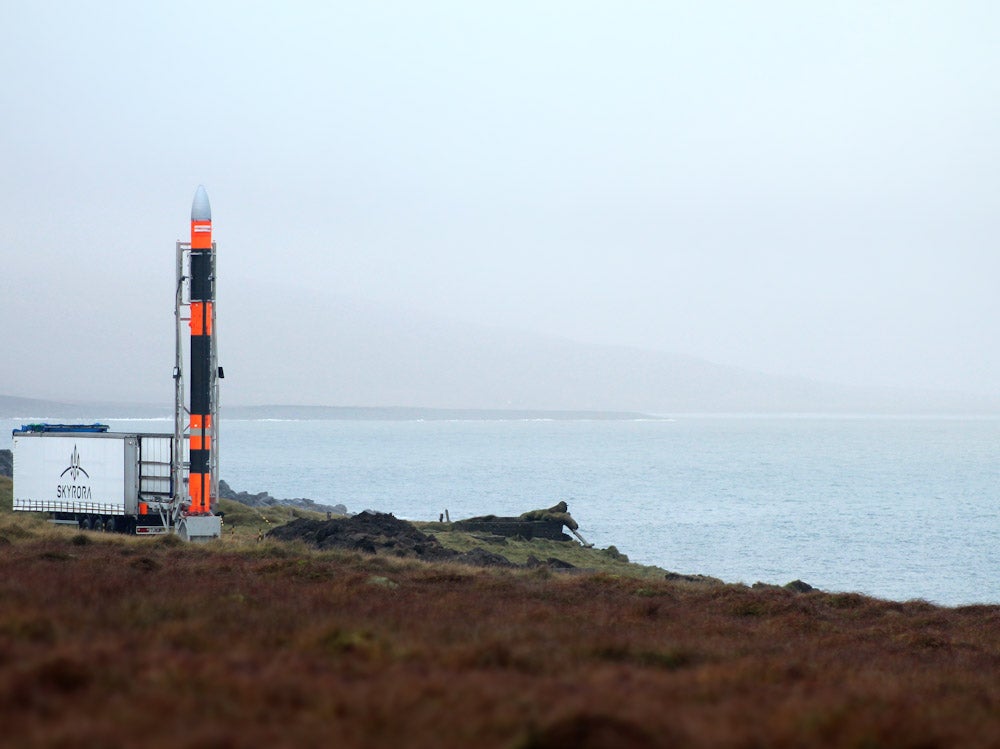
As a nickel-chromium superalloy often used in extreme environments, Inconel has many potential applications in space – but it remains expensive per kilo. However, using a 3D printer creates possibilities for new combinations of metals at lower costs. “If you are able to use half of that and then use steel or aluminium for printing, you have the same structural integrity,” says Harris. “It’s going to make things so much cheaper, which will hopefully then pass on to the consumers.”
In addition, Skyrora is working on rocket recovery and assessing how they can be reused after launches from Shetland’s SaxaVord spaceport. As the majority of recoveries will be from the sea, building rockets from Inconel has further advantages.
“It excites me that we are using Inconel because it is used in deep-sea oil pipes. So, the saltwater, shouldn’t cause as much damage,” says Harris. “Then it just comes down to how safely we can get the stages back to Earth – whether they ‘pancake’ or if they return in one piece.
“We are really looking forward to our next launch. When we recover the vehicle, we can see if the tanks and the engines are fit to be reused.”
3D-printed and reusable rockets
With a payload of up to 180kg, the Orbex Prime is a 19m-high vertical launch vehicle with two stages. The micro-launcher features seven engines and has been designed with a wide range of advanced materials. These include the use of additive manufacturing by 3D-printing most of the propulsion subsystem and carbon fibre composites for the main structures and tanks.
Orbex also uses 3D printing for entire rocket engines, which consist of a single unit without any joins. The company now has 3D printing facilities at its production centre in Forres, shortening supply chains dramatically.
The Prime rocket is designed for reuse. When it returns to Earth, the intention is to recover and reuse the majority of the rocket. Orbex is designing components that not only withstand the extremes of space, but saltwater as well.
“We had to choose the specific alloy for the engines because they must land in the sea. There is not enough room to carry enough fuel to try and do what SpaceX does with landing a vehicle,” adds Coates. “We had to design it so that you could drop it into the sea and recover it, including all the electronic systems.”
The importance of universities to Scotland’s space sector
Scotland is home to world-renowned universities that are an essential driver of innovation, providing both the talent and the research capabilities to deliver technological progress.
“We have got some of the brightest minds coming out of the universities that we’re able to hire,” says Harris.
“In Scotland, the technical abilities coming out of Herriot-Watt are second to none. We have had members of legal teams coming out of Glasgow University. We have had business teams coming out of Edinburgh. All the universities in Scotland have their different courses with their expertise.”
Furthermore, Skyrora has taken on two graduate apprentices as part of a national scheme in Scotland. The mix of education and industrial experience ensures apprentices are highly trained and have considerable experience with rockets when they graduate.
“When they get their full degree, they are probably some of the most experienced rocket techs in the country,” says Harris. “It’s an amazing scheme that we hope we can use more as we continue to grow.”
Along with benefitting from talent, Skyrora has worked on projects at universities that have enhanced technical understanding of processes and components. “We are in talks for things like turbopump engines to see how we can expand what is being done in the UK with technicalities and our staff,” says Harris.
Inspiring the next generation of space talent
Working alongside local businesses and the community is especially important to Orbex. The company has a designated liaison officer for local crofters and is involved in outreach programmes with local schools, taking on 12 interns last year.
Recent visits include Dallas Primary School and Forres Academy, as well as providing classroom resources for Dornoch Academy.
Coates highlights the importance of outreach programmes and STEM subjects for the engineers of tomorrow, noting that the Scottish expertise available has been vital.
Orbex also attracts talent from the oil & gas industry and the RAF, with a focus on specific expertise and management skills. Alongside its commitment to the local area, the company has a global reach.
“We hire a lot of local people, but obviously there are specialisms. We currently have 35 different nationalities in the company,” says Coates. “There is a whole range of factors in how you run a spaceport operation – preparing the vehicle, all the wet and dry testing – before you finally fill it up with the actual payload and off it goes.
“You must be incredibly careful about what you are doing, especially in the middle of an environmentally sensitive area. It is all about doing our best to protect the environment while we get on with the main job of rocket science.”
To learn more about how the space sector is developing in Scotland, download the document below.