Covid-19 has, of course, had an immense impact on health, society, industry and economies. Just three months before the first wave started to sweep the globe in 2020, it had practically never been heard of. Yet as soon as it emerged, entire industries were shut down while others were severely disrupted. Workers on mass were directed by governments not to travel, or to work from home wherever possible, and those that had underlying health conditions were forced to self-isolate. It felt like the world as we knew it was turned upside-down overnight. Businesses had no experience of such calamity, nor had they any contingency plans that came anywhere close to being adequate. The rule books were simply torn up.
Most businesses had to adapt on the fly, and rapidly. Every day came with another fire to fight, and as soon as the fires were out, along came the next Covid-19 wave or variant. As a result, manufacturers had to rapidly change their operations in response to supply and demand chain volatility or workforce availability. Changes to technology platforms to support remote workers had to be implemented in weeks, if not days. There was no time for proper planning, feasibility studies, risk assessments, or preparing a detailed business case with return-on-investment projections. Change simply had to happen quickly.
Learning from past mistakes
The past two years have taught us two key things. First, the impact of the pandemic will be with us for some time to come, perhaps indefinitely. Even with the UK government announcing that all Covid restrictions in England will end at the beginning of March, all it will take is another variant of concern to reignite conversations about restrictions and lockdowns.
Second, the proverbial black swan events can, and indeed will, happen eventually. That means that we not only need to make permanent some of the rapid changes recently made, and make them more robust and operationally sound, but we need to rethink many parts of our business operations. How flexible are they? How robust are they? And how are they able to support other future events that may have an unprecedented impact on business? Not just in terms of another pandemic, but from other possible disruptive events such as terrorist activities, natural disasters, economic crashes, geopolitical breakdowns, major trade wars, and so on.
For manufacturers, this ultimately means the optimisation of their operations to ensure that they are efficient, agile and robust.
Moving manufacturing towards a post-pandemic strategy
I believe that 2022 will be the year in which businesses of all sizes and across all industries move from the firefighting era of the pandemic response to an era of operational change and restructuring in the form of a post-pandemic strategy.
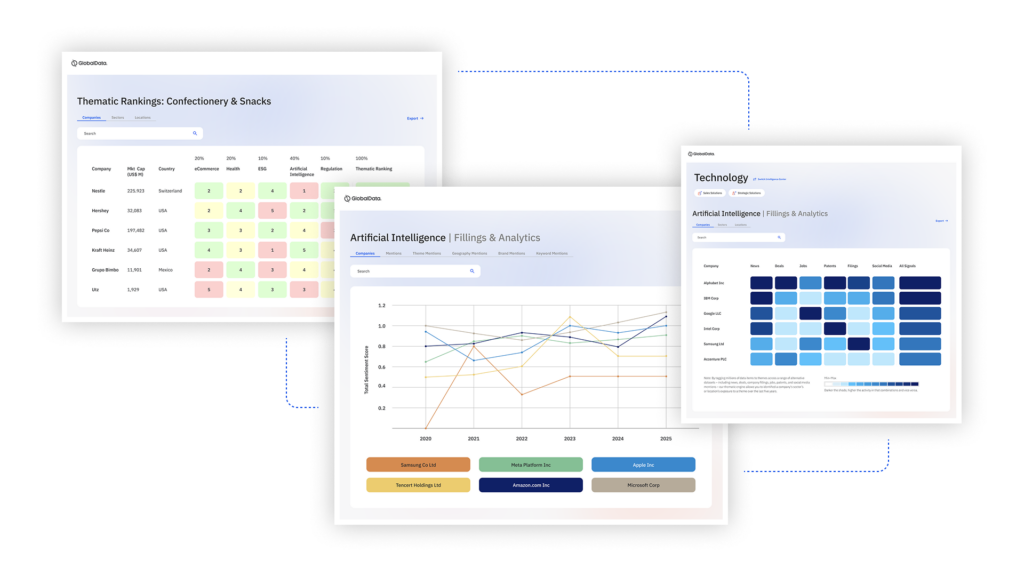
US Tariffs are shifting - will you react or anticipate?
Don’t let policy changes catch you off guard. Stay proactive with real-time data and expert analysis.
By GlobalDataThere are a plethora of ways this can be achieved. The way forward is for manufacturers to learn from the crisis and proactively identify pain points and weak points across their operations. These may include challenges around access to data, decision-making resources or simply initial response plans to major disruptions. From this understanding, it is possible to work through sustainable, tactical improvements to eliminate these risks and constraints, including through the effective use of technologies. Organisations can then build a vision for the future with a pipeline of short and long-term transformation opportunities that outline a path, from recovery to thriving in the post-pandemic world.
Digital transformation is the key
Once a lower priority on company budgets and agendas, digital transformation has over the past two years been pushed to the forefront of investment, especially among those who found deficiencies in their technology and infrastructure, which impaired their ability to respond and pivot operations when the outbreak began. Now, more manufacturers want to create nimble, flexible and proactive manufacturing environments – driven by data. It indicates a remarkable shift from the investments in electro-mechanical automation seen over recent decades, which primarily focused on improving efficiency and productivity.
We can now do more than automate manufacturing. We can optimise processes, giving manufacturers intelligent means of understanding what is happening on the plant floor so they can make informed decisions to drive enhancements and adjust operations accordingly. Those who can readily collect, centralise, analyse and act on real-time quality data will be the ones best equipped to recognise and navigate any future disruptions.