
Traditional manufacturing has undergone first, second and third ‘industrial revolutions’, all of which shared the ambition of increasing the use of innovative technologies to streamline production processes and attain best practice.
Now, the world is in the midst of the fourth industrial revolution, also known as industry 4.0. This transformation in manufacturing is ever-evolving as new technologies become available. While this pace of change can be dizzying, one thing is certain: a failure to adapt to and embrace the advantages of industry 4.0 can be a costly – and possibly lethal – mistake for companies and investors alike.
Discover B2B Marketing That Performs
Combine business intelligence and editorial excellence to reach engaged professionals across 36 leading media platforms.
In order to understand industry 4.0, it is useful to revise the revolutions that came before.
The first industrial revolution
Occurring roughly between 1760 and 1840 in Europe and North America, the first industrial revolution moved production from homes to factories and essentially created the manufacturing sector at industry level. This was underpinned by the agricultural revolution, which also saw its production escalate significantly with a huge increase in food output supporting the expansion.
The increase of machine use in farm work meant that fewer farm workers were needed, freeing them to leave the countryside and move to more industrial towns.
Steam and water power saw hand production methods switch to machine production, comprehensively changing the iron industry and the agricultural and mining sectors. These developments worked to the benefit of the European ‘powers’ and their respective growing empires. This was the beginning of the man and machine industry that is so prevalent today, with the balance between the two in the manufacturing sector still a topic of much debate.
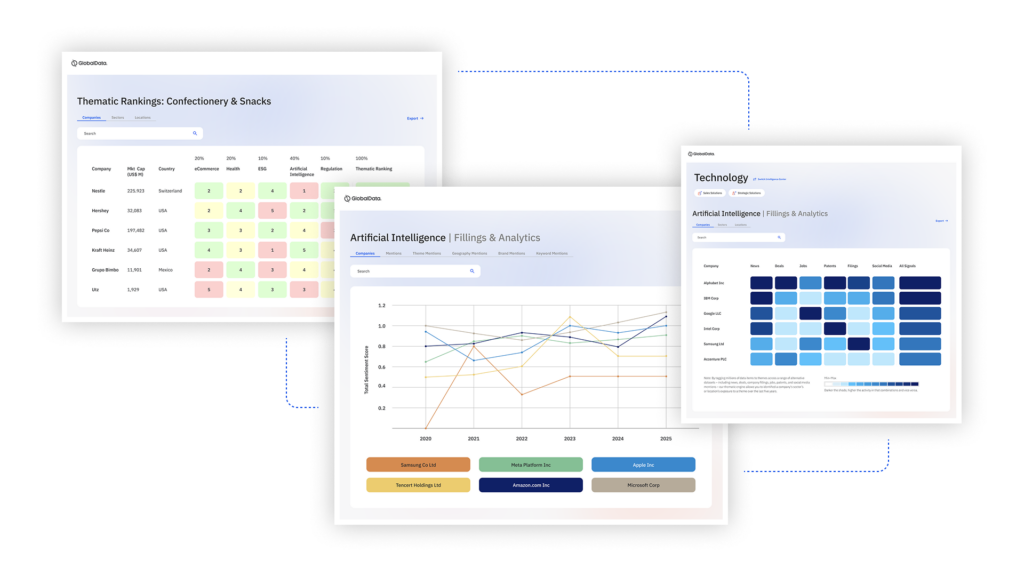
US Tariffs are shifting - will you react or anticipate?
Don’t let policy changes catch you off guard. Stay proactive with real-time data and expert analysis.
By GlobalDataThe second industrial revolution
The second industrial revolution, also known as the technological revolution, is dated roughly between 1870 and the start of the First World War in 1914 – although a number of crucial innovations to manufacturing for this period can be traced back to the 1850s.
Telephones, petroleum and electrical power grew in popularity and advances in mass steel production – notably through the Bessemer process – saw railroads expanded and more industrial machines built.
This period also increased automation as more machinery was implemented into factory working, principally through the introduction of the internal combustion engine.
Alongside increased connectivity through railroads, the invention of automobiles, the radio and telegraphs increasingly improved the accessibility of manufacturing and grew its supply chain. This period also saw improvements in the quality of life of the working classes, with cities building sewers and improving sanitation. Alongside this was an expansion of the middle class, as prosperity was shared more widely than had been the case in the first industrial revolution.
The third industrial revolution
The third industrial revolution, or the digital revolution, occurred in the late 20th century and some argue that it is still ongoing. Economist and author of the The Third Industrial Revolution, Jeremy Rifkin, states that the world is now living in “the carbon era”, with fossil fuels seeing accelerated use on a global scale.
Notably in this period, the invention of z1 – a motor-driven mechanical computer designed by Konrad Zuse – paved the way for more advanced digital developments. The internet and the supercomputer followed, and with them heightened artificial intelligence, or AI. As a result, there was even more use of computer and communication technologies throughout manufacturing and production as these practices became more normalised on a global scale.
So what is industry 4.0?
The phrase ‘industry 4.0’ was first introduced by Klaus Schwab, the founder and executive chairman of the World Economic Forum. He described it as “a range of new technologies that are fusing the physical, digital and biological worlds, and impacting all disciplines, economies and industries”.
Rifkin also stated that industrial revolutions can be characterised by technical advancements in three main areas – communications, energy and transport/logistics.
All three of these categories have been accelerated through the enhanced adoption of automation technologies, according to Deloitte UK industry 4.0 lead Nick Davis.
“We have been through a series of industrial revolutions, the most recent one being this degree of automation,” he says. “The fourth industrial revolution is about bringing a lot more intelligence into how technology is used in manufacturing in particular, and a convergence of digital technologies. So things like the use of the cloud, the internet of things, AI and these various different forms make manufacturing production more optimised in terms of efficiency and more sustainable in terms of low impact on the environment.”
All about the innovation
At its heart, industry 4.0 appears to be about innovation, and not unlike the revolutionary periods that came before it, it remains focused on how to strive for best practice. It poses critical questions for the manufacturing sector such as:
• How can advanced technologies to reinvigorate production be embraced?
• How can further automation accelerate productivity and cut costs without taking steps back in sustainability?
• What existing technologies can be enhanced to give more visibility to supply chains and enhance capacity capabilities on the ground?
• What skills will be needed as industry 4.0 continues to transform the manufacturing sector’s workforce requirements?
To many, industry 4.0 feels more holistic than its industrial revolution predecessors, in part because of the collaborative yet competitive environment it creates. To take advantage and control of an industry 4.0 manufacturing strategy requires vision, foresight and a new set of skills that perhaps weren’t as important within the sector during the previous periods.
Manual skills, although still relevant, are arguably no longer of primary importance for the sector; instead, new educational concepts carry weight such as the ability to scale IT infrastructures, to code and to analyse big data.
Davis recognises that industry 4.0 can be difficult to quantify and measure and that this can cause discord between the varying levels of the revolution.
“There is a lot of discussion about whether [collectively] we are at the start or midway through [this revolution] and so on. I think the maturity of different organisations varies hugely in terms of their adoption of these different concepts,” he says. “It can be difficult to pinpoint where exactly [manufacturing entities] are on the curve of industry 4.0.”
Deloitte’s 2019 Global Readiness Report further substantiates this theory, indicating that a lack of rounded, long-term industry 4.0 strategies holds many companies back from harnessing the full potential that the technology offers.
In Deloitte’s report, a large majority of industrial product leaders from the Europe, Middle East and Africa region expressed that they were unprepared for industry 4.0 adoption. Only 13% said that their companies had a comprehensive industry 4.0 strategy as of 2020.
What technologies make up industry 4.0?
Industry 4.0 manufacturers are often referred to as ‘smart factories’ due to their use of advanced technology. These can be grouped into four main categories:
• Cyber-physical systems
• The internet of things
• Cloud computing
• Cognitive computing.
Under these umbrella groups there are numerous digital technologies that are imperative to industry 4.0, including location detection technologies, 3D printing, smart sensors and advanced human-machine interfaces, among others.
These technologies offer many advantages, such as the ability to create a virtual copy of the physical world to make decentralised decisions and the ability to provide predictive maintenance.
Value in manufacturing implementation
Manufacturing, like industry 4.0, also seems to be a ‘slow burn’ when it comes to mapping progress. Deloitte and the Manufacturers Alliance for Productivity and Innovation released a joint study in 2019 focusing upon smart factories. This showed that global labour productivity had slowed in recent years: between 1987 and 2006 it averaged 3.6%, dropping to 0.7% between 2007 and 2018.
The report concludes that every manufacturer – whether they were already adopting smart factory practices or not – would gain business value from implementing smart factory initiatives. In the report, companies that had adopted industry 4.0 technologies reported an average gain of 10–12% in areas such as manufacturing output, factory utilisation and labour productivity. Furthermore, the report reports that so-called ‘trailblazers’ – those leading the charge in the utilisation of new technologies – were continually outperforming peers who weren’t as quick off the mark.
Deloitte UK’s Davis says: “[For trailblazers] it is not about just proof of concept to pilot within individual factories, but actually looking at multiple applications of digital within their manufacturing operations within factories, and also connecting with the broader network. [As a result,] they have much more visibility and the ability to flex production at a network level rather than just within individual factories.”
Davis also highlights the level of connectivity that the adoption of industry 4.0 brings to companies, not just within their manufacturing operations but to communication alignment overall.
“[Importantly, industry 4.0 increases] the extent of chief experience officer engagement within those organisations, where actually there is much more evidence or collaboration between chief information officers, chief technology officers, the chief financial officer, operations and so on.”
A workforce shift?
A heightened use of automation can often cause concern across labour-intensive industries that worker skill sets and roles within a factory environment are becoming obsolete.
It is true that the automation tools are designed to boost productivity at work and call for upskilling throughout the workforce. Therefore, workers are still key to enacting this change and will be required to adapt to the new technologies and feed into how these technologies can automate better.
Stephen Phipson, CEO of Make UK – a body that represents British manufacturers – believes that industry 4.0 actually calls for higher levels of employment.
“In many cases where we have seen factories installing automation [in the UK], we have seen an increase in their employment, not a decrease,” he says. “They have employed different types of people. They need different types of production engineers, coders, those sorts of things.”
Talented and tech-savvy workers are key to running smart factories and implementing successful 4.0 strategies. With this being the case, regions with high levels of innovative educational programmes have become extremely attractive to greenfield investors looking to revitalise their manufacturing operations.
The clear link between investment and industry 4.0-educated workforces has driven many governments to implement apprenticeship and scholarship programmes gearing up workers to enter the smart manufacturing work pool.
The 2019 IMD World Talent Ranking graded 63 countries on their ability and commitment to fostering a skilled and educated workforce, citing that a focus on educational programmes allowed for “long-term prosperity in a dynamic landscape where AI, robotics and other new technologies are redefining current and future challenges for business, policymakers and educational institutions”.
The report put Switzerland at the top of the overall ranking, with Denmark second. Sweden, Austria and Luxembourg took the third, fourth and fifth places, respectively, showing that Europe is ahead of the curve in nurturing attractive talent pools for investors.
FDI and industry 4.0
There is no denying that industry 4.0 has been disruptive to investor strategies for both inbound and outbound objectives, with production, governance and risk strategy being the most heavily impacted sections to reconsider. When considering foreign direct investment (FDI) all stakeholders are having to examine their roles carefully, assessing how industry 4.0 will affect their business models in both the short and medium term.
With industry 4.0’s excelled automation, cheap labour costs are no longer the bargaining chip they once were, and this levels the playing field between developing and developed countries. As a result, the way that greenfield investors select locations has changed, given the effect this has on the ways to rank the most cost-efficient factory locations. This could be seen as a negative for less-developed countries whose main attraction had been their cheaper labour costs.
Governments are now having to recognise this change in priority and enact policies that put the focus on prioritising technological literacy throughout the education system to nurture a new technically competent workforce. Developing innovative economies is now key to attracting inbound projects in a way that it wasn’t before.
A focus on breeding a creative sandbox environment – through tax credits and other incentives – for tech start-ups could also prove useful for developing countries looking to make themselves more attractive to would-be investors.
Industry 4.0 unapologetically calls for synergy between governments, businesses, educators and investors. As manufacturing continues towards further automation, and with rumblings of the advent of an industry 5.0, advances in technology ensure that the only option not open to manufacturers and investors alike is standing still.