
Economic indicators suggest that China’s manufacturing sector is showing signs of recovery following a massive government stimulus to the economy. The package, which was the biggest since the pandemic, aimed to halt deflation and foster growth.
A month after it was originally announced, Reuters reported that the government is considering issuing debt worth $1.4 trillion in the next few years.
The Caixin manufacturing purchasing managers index, by Caixin and S&P Global, rose 50.3 in October, compared to 49.3 in September. The reading followed the publication of official statistics saying that factory activity, which had been contracting for five months, picked up in October. The results exceeded analysts’ expectations.
“It’s very early days, but it’s certainly possible that the strong PMI readings reflect stimulus expectations,” according to Gavekal Dragonomics deputy China research director Chrisotpher Beddor.
“Policymaker are going to need to deliver on the actual fiscal stimulus in order to sustain any gains,” he added.
In September, China issued its 2024 negative list, outlining the industries where foreign investment is restricted or prohibited. The updated list removed two remaining restrictions on foreign investment in the manufacturing sector, according to state-owned media outlet Global Times.
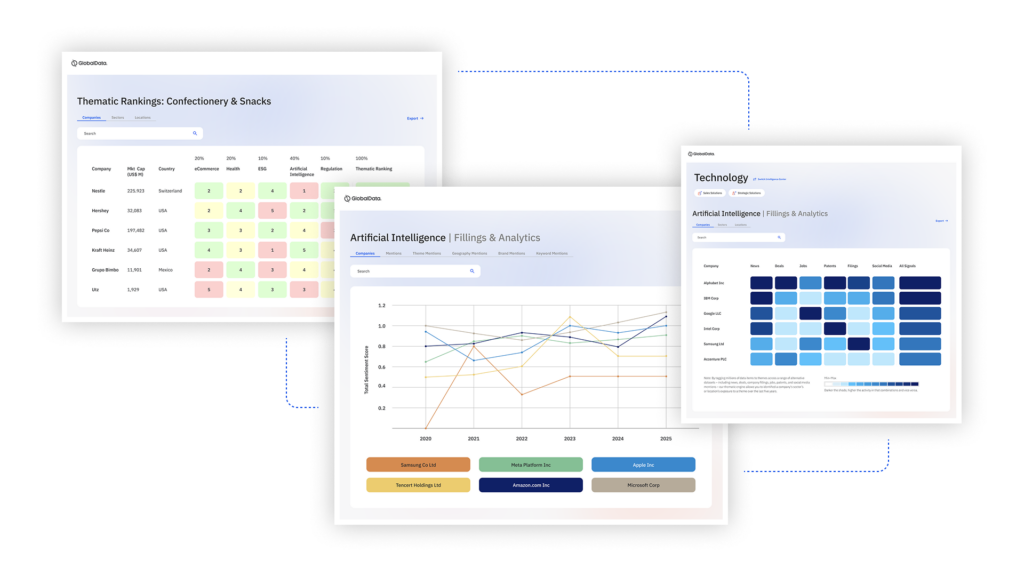
US Tariffs are shifting - will you react or anticipate?
Don’t let policy changes catch you off guard. Stay proactive with real-time data and expert analysis.
By GlobalDataThe remaining restrictions concerned the publication, printing, application and production of traditional Chinese medicine. The new list takes effect today (November 1).